Comprehensive Tank Welding Assessment for Industrial Safety and Regulatory Compliance
Making sure commercial safety and regulative conformity within the realm of storage tank welding assessments is a critical element of keeping functional integrity and mitigating prospective dangers. The thorough examination of weld high quality, material density, and total container condition is critical in securing versus architectural failings and environmental risks. By diving right into the details of comprehensive tank welding evaluations, a deeper understanding emerges of the diverse techniques used to promote sector criteria and maintain safety and security protocols.
Importance of Container Welding Inspections
Conducting regular and detailed container welding examinations is essential in ensuring the structural honesty, safety and security criteria, and regulative compliance of industrial tanks. These inspections play a crucial duty in recognizing any type of potential issues or weak points in the welded joints that could compromise the total stability of the storage tank. By spotting these issues beforehand, firms can take positive measures to resolve them immediately, thus avoiding pricey repair services, environmental contamination, or, in the worst-case scenario, tragic failures.
Normal storage tank welding inspections additionally assist companies follow industry laws and requirements established forth by authorities such as the American Oil Institute (API) or Occupational Safety and Wellness Administration (OSHA) Failing to meet these needs can result in penalties, legal effects, or even the suspension of procedures. Tank Welding Inspection Service. For that reason, spending in extensive container welding evaluations not just safeguards the well-being of workers and the surrounding setting but additionally protects the business's reputation and profits over time
Key Components of Weld Top Quality Assessment
Making sure the top quality of welds involves a careful evaluation of essential elements that add to the structural stability and dependability of commercial tanks. One important facet of weld quality assessment is the evaluation of weld infiltration. Correct infiltration is important as inadequate infiltration can bring about weld defects and compromise the stamina of the joint. Furthermore, the weld's account need to be analyzed to ensure that it meets the specified demands in terms of shapes and size. The existence of any type of interruptions, such as splits, porosity, or insufficient blend, have to be extensively inspected as these can weaken the weld and increase the likelihood of failure. Furthermore, the overall weld look is additionally a vital part of top quality analysis, as it can suggest the existence of problems or disparities in the welding process. By comprehensively evaluating these key parts, assessors can assist ensure that welded joints meet the essential criteria for security and regulatory compliance in commercial storage tank building.
Product Thickness Analysis Methods
In the context of weld quality evaluation, an integral element to consider is the use of product thickness analysis techniques. Exact measurement of material density is essential in making sure the structural stability and safety and security of welded storage tanks. Numerous non-destructive testing (NDT) techniques are used for assessing material density, consisting of ultrasonic testing, radiographic testing, and magnetic bit examination. Ultrasonic testing includes making use of high-frequency audio waves to identify material density by gauging the time taken for the sound waves to take a trip via the product and reflect back. Radiographic testing utilizes X-rays or gamma rays to create photos revealing worldly thickness. Magnetic particle evaluation is reliable for detecting surface and near-surface problems that may impact product density. These strategies not just aid in reviewing the thickness of materials but also aid in identifying any potential problems or gaps that might jeopardize the weld high quality and general stability of the storage tank framework. By utilizing these material thickness assessment methods, industries can guarantee compliance with safety standards and regulations, thereby boosting total functional security and dependability.
Storage Tank Problem Evaluation Methods
A necessary aspect in maintaining the integrity and security of welded containers is the extensive examination of storage tank conditions with dependable examination techniques. Container condition Get the facts exam methods play a critical function in making certain the structural sturdiness and operational effectiveness of commercial tanks. Aesthetic examination is a key method utilized to analyze the external condition of containers, looking for indications of deterioration, leaks, or physical damage. In addition, non-destructive screening techniques such as ultrasonic testing and radiographic screening are used to spot interior imperfections, weld defects, and material deterioration that might endanger the tank's performance. Tank Welding Inspection Service. Moreover, magnetic fragment examination can identify surface fractures and flaws that are not noticeable to the nude eye. These inspection methods offer useful understandings right into the total wellness of the container, enabling early detection of potential problems and assisting in prompt upkeep or fixings to make certain conformity with safety and security regulations and industry standards. Regular inspections using these approaches are essential for preventing catastrophic failures and Go Here ensuring the lasting integrity of bonded storage tanks.
Benefits of Routine Inspection Practices
Routine examination methods not just safeguard against possible issues found during storage tank problem examination techniques yet also act as aggressive measures in supporting the architectural honesty and operational effectiveness of bonded containers. By conducting regular assessments, commercial facilities can identify any type of indications of deterioration, cracks, leaks, or other flaws in the container welds without Full Report delay. This early discovery allows prompt fixings or upkeep treatments, avoiding little issues from escalating right into bigger, more expensive problems that can compromise security or bring about governing non-compliance.

Final Thought

To conclude, comprehensive storage tank welding examinations are important for making certain industrial safety and security and regulatory compliance. By carrying out regular assessments and analyses of weld top quality, product thickness, and container condition, organizations can recognize prospective dangers and avoid expensive crashes. Carrying out a proactive approach to assessment methods can assist maintain the architectural integrity of tanks, protect the environment, and make sure the safety of workers and the bordering neighborhood.
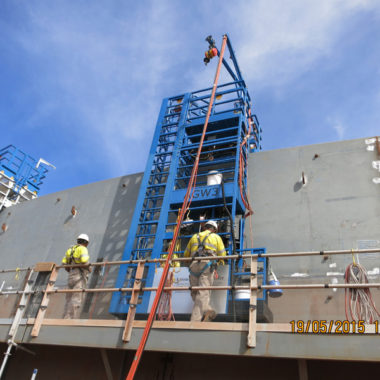